Electric motor
Q: I would like to know about any standard or documents or method, which will help to conduct accelerated life cycle test on electric motor. For example, if we are planning to give 10 years warranty on a motor, how long (short time) we should run the motor at rated condition to replicate the same impact. This is just an example.
A: First - you'd need to define the items that would be covered under such a warranty condition. Second - you'd need to decide what constitutes an acceptable failure rate during the warranty period.
For most manufacturers, this basically boils down to life cycle testing of a couple of key systems.
A: First - you'd need to define the items that would be covered under such a warranty condition. Second - you'd need to decide what constitutes an acceptable failure rate during the warranty period.
For most manufacturers, this basically boils down to life cycle testing of a couple of key systems.
Unlike other types of single-phase motors, shaded-pole motors have only one main winding and no start winding or switch. As in other induction motors, the rotating part is a squirrel-cage rotor. Starting is by means of a design that uses a continuous copper loop around a small portion of each motor pole. Currents in this copper loop delay the phase of magnetic flux in that part of the pole enough to provide a rotating field. This rotating field effect produces a very low starting torque compared to other classes of single-phase motors. Although direction of rotation is not normally reversible, some shaded-pole motors are wound with two main windings that reverse the direction of the field. Slip in the shaded-pole motor is not a problem, as the current in the stator is not controlled by a counter-voltage determined by rotor speed, as in other types of single-phase motors. Speed can therefore be controlled merely by varying voltage, or through a multitap winding.
Shaded-pole motors are best suited to low-power household application, because the motors have low starting torque and efficiency ratings. Because of the weak starting torque, shaded-pole motors are built only in small sizes ranging from 1/20 to 1/6 hp. Applications for this type of motor include fans, can openers, blowers, and electric razors.
Shaded-pole motors are best suited to low-power household application, because the motors have low starting torque and efficiency ratings. Because of the weak starting torque, shaded-pole motors are built only in small sizes ranging from 1/20 to 1/6 hp. Applications for this type of motor include fans, can openers, blowers, and electric razors.
First, 7 things to consider when choosing an electric motor:
Choosing the right motor isn’t always straightforward. There are so many variables to consider that it can be hard to know where to start. The wrong motor can result in a myriad of problems, and can ultimately cause application failure.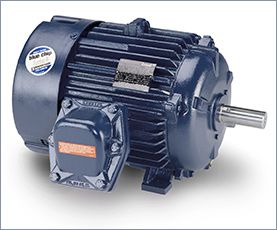
(Here are) some initial questions that you need to answer before attempting to find the right motor for your project.
Questions you need to consider in choosing a motor:
Choosing the right motor isn’t always straightforward. There are so many variables to consider that it can be hard to know where to start. The wrong motor can result in a myriad of problems, and can ultimately cause application failure.
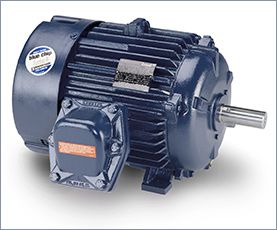
(Here are) some initial questions that you need to answer before attempting to find the right motor for your project.
Questions you need to consider in choosing a motor:
Speed: How fast should the motor be able to run? Torque: Which motors provide enough torque? Size: What are the size restrictions? Precision: Does the motor need to be accurate? How accurate? Environment: What is the environment in which the motor will be running (is there dust, moisture, air flow, etc.)? Communication: How do you want to communicate with the motor? Cost: What is your budget?
Once you’ve come up with answers to these preliminary questions, you can begin to figure out the best option for your application.
Motor Failed…Who Cares?
Too often we hear maintenance & reliability experts downplay the data analysis or testing of motors that have failed from a stator fault. "Why would you need test equipment to test a stator fault?" we might hear. The mistake these "experts" make is to assume that troubleshooting a motor begins with failure analysis. Smart motors are on the market, but we haven't seen any with a big red flag that pops up with the words "STATOR FAULT" when it trips or fails to start. The reality most non-clairvoyant technicians face is they don't know exactly what failed, or if anything failed at all. Is it the motor, the load, the starter or maybe a nuisance trip? Remember a very important role of your predictive technologies is to assist the technicians in a quick recovery effort of production in the unfortunate situation of an unplanned outage. Performing some quick tests such as phase resistance, phase inductance, and ground wall tests can allow the technician to isolate quickly focus on or off of the electric motor and hasten good decision-making in deciding if a repair or replacement is necessary. A simple phase imbalance test may just prevent you from replacing a motor that doesn't need to be replaced.
It's Not Always the Motor's Fault
When testing a motor it is good practice to thoroughly test the entire motor circuit. A Wound Rotor Motor has two circuits – the stator circuit, which is very similar to a standard AC induction motor, and a rotor circuit. The rotor circuit usually consists of rotor windings, rings and brushes, and a resistor bank controlled using contactors. Depending on the application, the rotor circuit is used to control the torque, speed, or startup current of the motor. The external portion of the rotor circuit usually consists of an external resistor bank with a number of resistance steps. An unbalance of resistance in the resistor bank will cause an unbalance of the flux in the rotor creating a situation similar to a broken rotor bar. There are several tests using the MCEMAX that can be performed to evaluate this situation. With the motor de-energized, a standard test can be performed on each step of the resistor bank circuit to ensure resistance is balanced through each step and when the resistor bank is fully shorted out. With the motor running, a rotor evaluation test can be performed to look for a current unbalance during startup and after the motor is at full speed. An In-Rush test can be used to evaluate startup and switching times when troubleshooting anomalies in the rotor circuit.
Too often we hear maintenance & reliability experts downplay the data analysis or testing of motors that have failed from a stator fault. "Why would you need test equipment to test a stator fault?" we might hear. The mistake these "experts" make is to assume that troubleshooting a motor begins with failure analysis. Smart motors are on the market, but we haven't seen any with a big red flag that pops up with the words "STATOR FAULT" when it trips or fails to start. The reality most non-clairvoyant technicians face is they don't know exactly what failed, or if anything failed at all. Is it the motor, the load, the starter or maybe a nuisance trip? Remember a very important role of your predictive technologies is to assist the technicians in a quick recovery effort of production in the unfortunate situation of an unplanned outage. Performing some quick tests such as phase resistance, phase inductance, and ground wall tests can allow the technician to isolate quickly focus on or off of the electric motor and hasten good decision-making in deciding if a repair or replacement is necessary. A simple phase imbalance test may just prevent you from replacing a motor that doesn't need to be replaced.
It's Not Always the Motor's Fault
When testing a motor it is good practice to thoroughly test the entire motor circuit. A Wound Rotor Motor has two circuits – the stator circuit, which is very similar to a standard AC induction motor, and a rotor circuit. The rotor circuit usually consists of rotor windings, rings and brushes, and a resistor bank controlled using contactors. Depending on the application, the rotor circuit is used to control the torque, speed, or startup current of the motor. The external portion of the rotor circuit usually consists of an external resistor bank with a number of resistance steps. An unbalance of resistance in the resistor bank will cause an unbalance of the flux in the rotor creating a situation similar to a broken rotor bar. There are several tests using the MCEMAX that can be performed to evaluate this situation. With the motor de-energized, a standard test can be performed on each step of the resistor bank circuit to ensure resistance is balanced through each step and when the resistor bank is fully shorted out. With the motor running, a rotor evaluation test can be performed to look for a current unbalance during startup and after the motor is at full speed. An In-Rush test can be used to evaluate startup and switching times when troubleshooting anomalies in the rotor circuit.
There are some customers out there that have their larger motors repaired at one facility and their smaller motors repaired at others. There are also customers who expect you to take care of all their motor repairs no matter how small or how large.
It has become increasingly difficult to make a profit by repairing smaller motors, so when they are standard / off the shelf motors there is a small profit to be made by replacing the motor as opposed to a loss when the motor is repaired. In the case of smaller Specialty or OEM motors the repair price is most often more expensive than new but sometimes the new motor has an extended delivery. In cases like this when delivery is a factor we give a fixed price prior to repair. In 99% of these cases the customer will tell us to proceed. The internet has made it much easier to source the OEM Motor and obtain a price and delivery quite quickly.
Where we will subcontract a repair to another facility is on the rewind of small armatures. Most of the larger facilities do not have the equipment required to economically rewind a small armature but there are some shops that specialize in that aspect of motor repair. we rarely encounter any problems when we subcontract this type of work. We do al the dismantling and assembly work that is required and we get a price ahead of time from the subcontractor. the customer gets the total price ahead of time and issues a purchase order or gives a verbal go ahead. The only time we run into problems is when the subcontractor does not meet the delivery date.
It has become increasingly difficult to make a profit by repairing smaller motors, so when they are standard / off the shelf motors there is a small profit to be made by replacing the motor as opposed to a loss when the motor is repaired. In the case of smaller Specialty or OEM motors the repair price is most often more expensive than new but sometimes the new motor has an extended delivery. In cases like this when delivery is a factor we give a fixed price prior to repair. In 99% of these cases the customer will tell us to proceed. The internet has made it much easier to source the OEM Motor and obtain a price and delivery quite quickly.
Where we will subcontract a repair to another facility is on the rewind of small armatures. Most of the larger facilities do not have the equipment required to economically rewind a small armature but there are some shops that specialize in that aspect of motor repair. we rarely encounter any problems when we subcontract this type of work. We do al the dismantling and assembly work that is required and we get a price ahead of time from the subcontractor. the customer gets the total price ahead of time and issues a purchase order or gives a verbal go ahead. The only time we run into problems is when the subcontractor does not meet the delivery date.
Introduction: As electrical professionals, many of us would have been handling electric motors in hundreds of numbers over the years in our careers. And, whatever the SI System of units might suggest, many of us would still prefer to refer to electric motors' power rating in horse power only rather than in watts or kilowatts as is prescribed in the SI System of units. But, how many of us know why this is so? Why electric motors are rated in horsepower? Why not in Elephant Power, as somebody asked this author?
The story: One would be surprised to note that the rating of electric motors in horsepower has nothing to do with any electrical professional in the first place. It all started with one James Watt. Recall him? He is a Scottish engineer, associated with the Steam Engine. In most of the children's general knowledge books, James Watt is wrongly credited with the invention of the Steam Engine. That credit goes to one Thomas Newcomen of England, who, in fact, had invented the Steam engine in 1705. James Watt only made improvements to the Newcomen Engine, to improve its efficiency and to make it commercially viable. This was in the year 1769.
Having made this improvement, Watt started manufacturing these engines, in a partnership with a businessman called Matthew Boulton and started looking for markets for his engine. Remember! It was the 18th century. And the industrial revolution was in its primitive stages in England. The main profession of world's population was only agriculture. The only customers, to whom Watt could sell his engine, were farmers. Watt started talking to farmers, with a view to market his engine to them. They wanted to know what his engine could do for them. Watt knew that an engine is a device that could do some work. What work that a farmer is more interested in? That of drawing water from a deep well and of irrigating his fields.
The story: One would be surprised to note that the rating of electric motors in horsepower has nothing to do with any electrical professional in the first place. It all started with one James Watt. Recall him? He is a Scottish engineer, associated with the Steam Engine. In most of the children's general knowledge books, James Watt is wrongly credited with the invention of the Steam Engine. That credit goes to one Thomas Newcomen of England, who, in fact, had invented the Steam engine in 1705. James Watt only made improvements to the Newcomen Engine, to improve its efficiency and to make it commercially viable. This was in the year 1769.
Having made this improvement, Watt started manufacturing these engines, in a partnership with a businessman called Matthew Boulton and started looking for markets for his engine. Remember! It was the 18th century. And the industrial revolution was in its primitive stages in England. The main profession of world's population was only agriculture. The only customers, to whom Watt could sell his engine, were farmers. Watt started talking to farmers, with a view to market his engine to them. They wanted to know what his engine could do for them. Watt knew that an engine is a device that could do some work. What work that a farmer is more interested in? That of drawing water from a deep well and of irrigating his fields.
Theoretically, Yes, if the conditions under which it's running are constant (on squirrel cage induction motors). In reality, it varies due to a variety of factors. These can include changes in load, input power, environmental conditions, etc. Speed control really has 2 effects - providing a wider range of speed capabilities with the same motor (adjustability) as well as smoothing out (or at least attempting to smooth out) the effects that would change the motor speed and transients in loading, input voltage, etc.
Practically, NO, for electric motors connected to the AC power line. The speed of an AC induction motor is a function of the AC frequency, the number of poles in the motor, and the load on the motor. Under no-load conditions, the speed is quite constant. Under load, the speed will vary since the motor torque comes from the lag in the phase current. Unless the motor runs slower than synchronous speed, it cannot produce the torque necessary to do its work. Synchronous motors run at constant speed.
Practically, NO, for electric motors connected to the AC power line. The speed of an AC induction motor is a function of the AC frequency, the number of poles in the motor, and the load on the motor. Under no-load conditions, the speed is quite constant. Under load, the speed will vary since the motor torque comes from the lag in the phase current. Unless the motor runs slower than synchronous speed, it cannot produce the torque necessary to do its work. Synchronous motors run at constant speed.
Induction motors operate on the principal of current induction in the rotor which must rotate at a speed less than synchronous speed for induction to occur. This is referred to as slip speed and should not be confused with pole slipping.
Why induction motors have no pole slipping and why other motors have pole slipping. I will attempt to answer this but first let's define poles and synchronous speed in regards to electric motor operation.
Poles in an electric motor refer to the magnetic circuit poles and come in sets of two just like a common magnet. One is north (N) and one is south (S). If a motor has two poles, it will have one N-pole and one S-pole. If the motor has four poles, it will have 2 N-poles and 2 S-poles and so on.
Synchronous speed in an electric motor is the speed that is produced by the traveling magnetic filed wave as it rotates around the stator magnetic circuit. The synchronous speed of a motor is equal to 120*f/p where f = the system frequency in Hz and p is equal to the number of poles in the motor.
All AC motors have two basic parts: (1) a stator winding and iron core and (2) a rotor winding and iron core that is free to rotate and is connected to the motor shaft. For a 3-phase induction motor, when the stator is energized by a three phase voltage source, a magnetic field will be produced that rotates at synchronous speed. As this magnetic flux cuts across the rotor winding it induces a current (via Faraday's law of induction) in the rotor winding which intern produces a second magnetic flux. These two magnetic fluxes both rotate at synchronous speed and couple together like two magnets and thus transfer torque directly to the rotor shaft.
Why induction motors have no pole slipping and why other motors have pole slipping. I will attempt to answer this but first let's define poles and synchronous speed in regards to electric motor operation.
Poles in an electric motor refer to the magnetic circuit poles and come in sets of two just like a common magnet. One is north (N) and one is south (S). If a motor has two poles, it will have one N-pole and one S-pole. If the motor has four poles, it will have 2 N-poles and 2 S-poles and so on.
Synchronous speed in an electric motor is the speed that is produced by the traveling magnetic filed wave as it rotates around the stator magnetic circuit. The synchronous speed of a motor is equal to 120*f/p where f = the system frequency in Hz and p is equal to the number of poles in the motor.
All AC motors have two basic parts: (1) a stator winding and iron core and (2) a rotor winding and iron core that is free to rotate and is connected to the motor shaft. For a 3-phase induction motor, when the stator is energized by a three phase voltage source, a magnetic field will be produced that rotates at synchronous speed. As this magnetic flux cuts across the rotor winding it induces a current (via Faraday's law of induction) in the rotor winding which intern produces a second magnetic flux. These two magnetic fluxes both rotate at synchronous speed and couple together like two magnets and thus transfer torque directly to the rotor shaft.
Permanent Magnet motors are more efficient than SCIM as the field in the rotor is permanently there. The big advantage for permanent magnet motors is in the low RPM variable speed applications that run in the 300 to 600RPM maximum speed range. (ie. Draft fans and Slurry Pumps) Traditional these applications used a 16 to 20 pole SCIM or a 4 Pole motor with a gearbox. The cost of these two traditional solutions is close to the PM solution but supplied in a much smaller package and you do not have the efficiency loss or maintenance cost of a gear box to worry about. The negative side of permanent magnet motors is they do not like to be operated above rated speed as PM rotor causes the voltage to increase proportionally with speed, therefore over voltage above base speed.
As long as RE prices remain at or near their current levels, the potential of the PMSM market will be limited and adoption rates will remain low due to cost sensitivity. Based on the latest round of export quota tightening on behalf of the Chinese (2012 quota is to be 27% less than 2011), I don't see this changing in the near future. The best reprieve is 2-3 years away, when other RE mines that are re-opening start producing meaningful quantities.
As long as RE prices remain at or near their current levels, the potential of the PMSM market will be limited and adoption rates will remain low due to cost sensitivity. Based on the latest round of export quota tightening on behalf of the Chinese (2012 quota is to be 27% less than 2011), I don't see this changing in the near future. The best reprieve is 2-3 years away, when other RE mines that are re-opening start producing meaningful quantities.
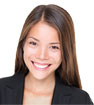


Category
Featured
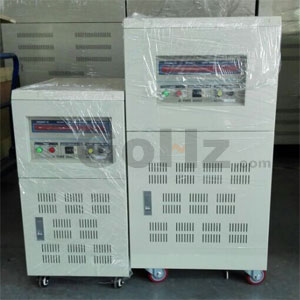
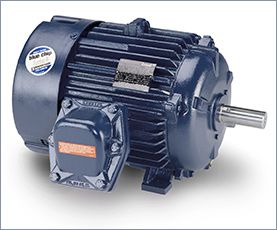
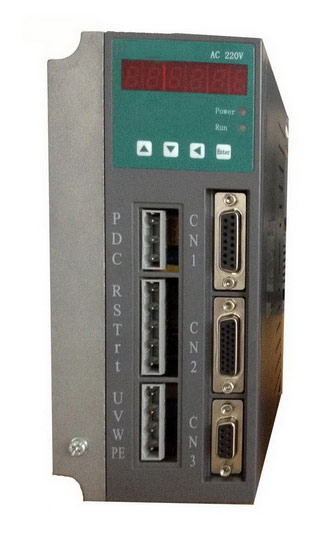