PM motor
It's important first to understand BLPM motors. There are several types that operate in a different way and some very good text books on the topic are Hendershot & Miller (2010) or Hanselman (2004).
If you deal with radial flux BLPM motors, anaytical packages such PC-BDC (SPEED) can give you very good results for surface PM motors, while for interior PM motors FEA is absolutely necessary, e.g. PC-FEA which is embedded in SPEED . Most of the finite-element packages will give you similar results, difference is made in price, computation time and easiness of usage.
Last, but not least, thermal aspects in BLPM are usually neglected even though magnets will demagnetise with temperature leading to higher current and lower efficiency for the same output. FEA will fail to give you a good estimation of the motor thermal behavior being capable of modelling just conduction. MotorCAD can solve the thermal problems and is linked to SPEED.
For axial flux motor you will need to go into 3D FEA. There are several analytical approaches developed at various Universities worldwide.
There are a lot of subtleties to designing BLPM motors, some not immediately obvious, particularly if you want an IPM motor with wide field weakening or something. It is often easy to get something that will do, but hard to get a really good design that is high efficiency and maximizes the material. FEA software, even ones with front ends for entering geometrical data, will have more limited options and gives one answer; the time it takes to vary parameters and formulate an effective design can be very long. SPEED is a spreadsheet entry package with many powerful design options and routines, It is by far more sophisticated than any of the FEA packages in terms of design variety. RMXpert is simply an FEA bolt on.
If you deal with radial flux BLPM motors, anaytical packages such PC-BDC (SPEED) can give you very good results for surface PM motors, while for interior PM motors FEA is absolutely necessary, e.g. PC-FEA which is embedded in SPEED . Most of the finite-element packages will give you similar results, difference is made in price, computation time and easiness of usage.
Last, but not least, thermal aspects in BLPM are usually neglected even though magnets will demagnetise with temperature leading to higher current and lower efficiency for the same output. FEA will fail to give you a good estimation of the motor thermal behavior being capable of modelling just conduction. MotorCAD can solve the thermal problems and is linked to SPEED.
For axial flux motor you will need to go into 3D FEA. There are several analytical approaches developed at various Universities worldwide.
There are a lot of subtleties to designing BLPM motors, some not immediately obvious, particularly if you want an IPM motor with wide field weakening or something. It is often easy to get something that will do, but hard to get a really good design that is high efficiency and maximizes the material. FEA software, even ones with front ends for entering geometrical data, will have more limited options and gives one answer; the time it takes to vary parameters and formulate an effective design can be very long. SPEED is a spreadsheet entry package with many powerful design options and routines, It is by far more sophisticated than any of the FEA packages in terms of design variety. RMXpert is simply an FEA bolt on.
PM (Permanent Magnet) motor, which has a flux that cannot be turned off. So, you should make sure your power electronics can handle the max back EMF corresponding to max speed of the motor. If you require flux weakening at top speed to reduce the Vemf, you should make sure you can handle that full Vemf if you lose that direct axis current.
The second item is to have a "per unit inductance machine", meaning that the flux linkage and inductance are designed such that if the machine shorted to DC neg reference, the current would not exceed rating of your transistors.
(Isc=V/Z~Vemf/w*L=(w*Lambda)/(w*L)=Lambda/L)---> Isc = Lambda/L
The second item is to have a "per unit inductance machine", meaning that the flux linkage and inductance are designed such that if the machine shorted to DC neg reference, the current would not exceed rating of your transistors.
(Isc=V/Z~Vemf/w*L=(w*Lambda)/(w*L)=Lambda/L)---> Isc = Lambda/L
Permanent Magnet motors are more efficient than SCIM as the field in the rotor is permanently there. The big advantage for permanent magnet motors is in the low RPM variable speed applications that run in the 300 to 600RPM maximum speed range. (ie. Draft fans and Slurry Pumps) Traditional these applications used a 16 to 20 pole SCIM or a 4 Pole motor with a gearbox. The cost of these two traditional solutions is close to the PM solution but supplied in a much smaller package and you do not have the efficiency loss or maintenance cost of a gear box to worry about. The negative side of permanent magnet motors is they do not like to be operated above rated speed as PM rotor causes the voltage to increase proportionally with speed, therefore over voltage above base speed.
As long as RE prices remain at or near their current levels, the potential of the PMSM market will be limited and adoption rates will remain low due to cost sensitivity. Based on the latest round of export quota tightening on behalf of the Chinese (2012 quota is to be 27% less than 2011), I don't see this changing in the near future. The best reprieve is 2-3 years away, when other RE mines that are re-opening start producing meaningful quantities.
As long as RE prices remain at or near their current levels, the potential of the PMSM market will be limited and adoption rates will remain low due to cost sensitivity. Based on the latest round of export quota tightening on behalf of the Chinese (2012 quota is to be 27% less than 2011), I don't see this changing in the near future. The best reprieve is 2-3 years away, when other RE mines that are re-opening start producing meaningful quantities.
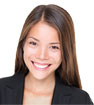


Category
Featured
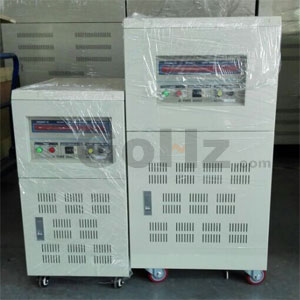
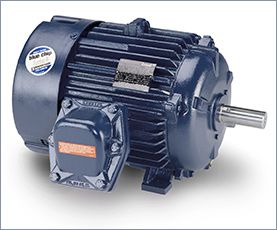
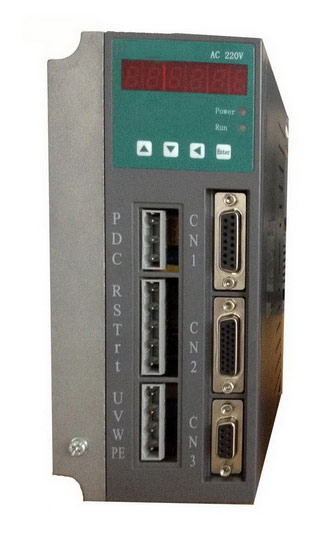