Servo drive
Q: I have used only the position control mode only in the servo drive. Can anyone please explain me about speed/velocity control mode in the servo drive, like for the position control mode we will be giving pulse and direction from the external controller, likewise which thing we need to give for speed control mode?
A: Position control in servo motor mean the motor will travel a defined position with some speed. In Position mode u can control both distance & speed by using controller. Position control is used in applications where more accuracy is needed. In Velocity control mode, the speed is controlled by controlling the voltage (0-10V) through external Pot. It is used in a place where controlling is Analog.
For velocity control, you just need to induce an analog signal on the servo drives terminals, and also a zero input command for some brands. This is a lot easier than the position control mode. It's like treating it as an AC variable frequency drive (VFD), only that the servo motor responds more accurately on different speed commands.
A: Position control in servo motor mean the motor will travel a defined position with some speed. In Position mode u can control both distance & speed by using controller. Position control is used in applications where more accuracy is needed. In Velocity control mode, the speed is controlled by controlling the voltage (0-10V) through external Pot. It is used in a place where controlling is Analog.
For velocity control, you just need to induce an analog signal on the servo drives terminals, and also a zero input command for some brands. This is a lot easier than the position control mode. It's like treating it as an AC variable frequency drive (VFD), only that the servo motor responds more accurately on different speed commands.
I was doing some tests the other day on slow speed control (1rpm). I thought that sinusoidal commutation and a high resolution encoder (4K CPT) would be "the thing" for controlling a multi-pole flat motor well (with detent torque - naming the EC90 flat from maxon). This would enable the controller to have better control during the commutation between coil switching. During the commutation the natural attraction of the rotor to the poles pulls and pushes the rotor into position. This is something that I thought sinusoidal commutation would help with. I was pleasantly surprised that using another controller that had just block commutation but a 53.5Khz current loop proved far superior in comparison to the 10KHz control on the sinusoidal drive!
A servo system is a servo system and so where or how it is used, not to oversimplify, it is almost irrelevant to a controls engineer. There are a lot of questions that would have to be answered before either myself or anyone with experience in controls could give you sound advice specific to your project:
This is just to get you started thinking about some basic issues. I have experience with motion controls, but I am not a motion controls expert. A motion controls expert will I am sure, come up with a much more comprehensive list of questions.
As far as servos, if you are looking to learn how to program motion controls, I suggest to look into Yaskawa. Spend a few hours perusing their website. Yaskawa products have very good reputation and they have a large installed base, and, I personally like their website. It has a lot of useful information. I like Allen-Bradley as well, but you should know that I am an Allen-Bradley integrator and channel partner, and so I am somewhat partial to their products. AB stuff is expensive anyway, but for good reason. One of my colleagues for whom I have tremendous respect, with a ton of experience in motion controls is very fond of Copley.
If you Google 'Motion Controls' you'll get a ton of hits and you should find some useful info there as well.
Generally speaking, in my opinion, a big part of anything involving motion; fault handling and recovery, and of course, safety. You absolutely must take safety into consideration when dealing with motion and make it a priority.
- Do you already have an EMAP Servo Press?
- Does it have a servo control system in it already?
- If it does, are you looking to integrate the Press with other automation devices?
- If it doesn't, how many axes do you need?
- Do you need a coordinated motion controller?
This is just to get you started thinking about some basic issues. I have experience with motion controls, but I am not a motion controls expert. A motion controls expert will I am sure, come up with a much more comprehensive list of questions.
As far as servos, if you are looking to learn how to program motion controls, I suggest to look into Yaskawa. Spend a few hours perusing their website. Yaskawa products have very good reputation and they have a large installed base, and, I personally like their website. It has a lot of useful information. I like Allen-Bradley as well, but you should know that I am an Allen-Bradley integrator and channel partner, and so I am somewhat partial to their products. AB stuff is expensive anyway, but for good reason. One of my colleagues for whom I have tremendous respect, with a ton of experience in motion controls is very fond of Copley.
If you Google 'Motion Controls' you'll get a ton of hits and you should find some useful info there as well.
Generally speaking, in my opinion, a big part of anything involving motion; fault handling and recovery, and of course, safety. You absolutely must take safety into consideration when dealing with motion and make it a priority.
A servo drive system, as opposed to a variable frequency drive (VFD) or AC motor drive (AMD), has the ability to position with extreme precision and repeatability. While a VFD or AMD can be configured for position control, it cannot attain the exactness of a servo drive. VFD's and AMD's are also available in much higher horsepower ranges than servo's. Selection of external feedback sensors such as encoders, resolvers, linear position sensors, etc., required to achieve closed-loop control and each having its own inherent precision, will enable the system accuracy accordingly. Your application requirements will always dictate which system configuration will give you the best results!
Many of today's VFDs are fully capable of doing positioning when using encoder feedback; as with many other things, the lines have become blurred. What separates servo motor from induction motors is their low inertia and their ability to accelerate and decelerate much faster, the trick is to decide when you need full servo performance.
Many of today's VFDs are fully capable of doing positioning when using encoder feedback; as with many other things, the lines have become blurred. What separates servo motor from induction motors is their low inertia and their ability to accelerate and decelerate much faster, the trick is to decide when you need full servo performance.
Gozuk synchronous ac servo drive is designed and manufactured, employing the advanced control algorithm based on the market demand, which can realize speed and accurate position digital control. With intelligent power module (IPM) and other latest technology design, simple operation, high reliability, small size, easy to install.
Cover a big range of servo motor which up to 5.5KW.
Gozuk servo drive has mature servo technology and the highest cost performance.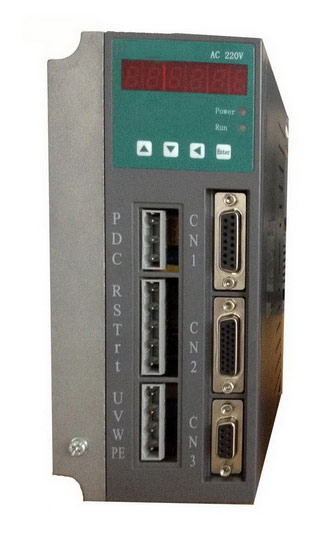
Servo Drive Features:
Speed range: Steady speed operation of the highest speed up to 5000 RPM, minimum speed 0.1 RMP.
Overload ability: torque can be up to 3 times of the rated load.
High dynamic response: speed loop bandwidth can reach 300 hz, process and load speed change little.
Input/output terminal: light coupling isolation, functional programmable, input terminal can realize servo enabled, alarm clear, torque limit and emergency stop, and other functions, output terminal can be controlled with switch, relay and open collector triode, using Darlington photoelectric coupler for output, can be connected with relay and photoelectric coupler, interfaces are more convenient to use.
Analog command control: speed, torque Shared a analog control, can difference or single-ended input, range - 10 v ~ + 10 v.
Position control mode: high speed light coupling isolation plus/signal signals, CCW/cw + signal and A/B phase + signal control mode, and employs the difference or single-terminal pulse receive mode, can effectively restrain the interference, optional instruction pulse smooth filtering, make the system in deceleration process smooth operation, increase the pulse signal digital filter and detection way.
Resonance inhibition: the servo drive can rise to inhibit resonance effect by adjusting the internal parameters
Encoder signal output: encoder signal frequency division and then drive output through line
Protection function: over voltage, over current, overload, overspeed and encoder anomaly and other kinds of error detection mechanism, nip in the bud.
Cover a big range of servo motor which up to 5.5KW.
Gozuk servo drive has mature servo technology and the highest cost performance.
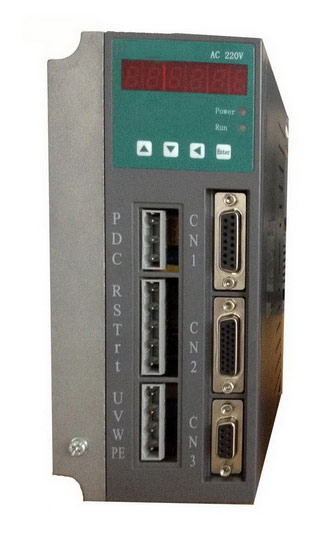
Servo Drive Features:
Speed range: Steady speed operation of the highest speed up to 5000 RPM, minimum speed 0.1 RMP.
Overload ability: torque can be up to 3 times of the rated load.
High dynamic response: speed loop bandwidth can reach 300 hz, process and load speed change little.
Input/output terminal: light coupling isolation, functional programmable, input terminal can realize servo enabled, alarm clear, torque limit and emergency stop, and other functions, output terminal can be controlled with switch, relay and open collector triode, using Darlington photoelectric coupler for output, can be connected with relay and photoelectric coupler, interfaces are more convenient to use.
Analog command control: speed, torque Shared a analog control, can difference or single-ended input, range - 10 v ~ + 10 v.
Position control mode: high speed light coupling isolation plus/signal signals, CCW/cw + signal and A/B phase + signal control mode, and employs the difference or single-terminal pulse receive mode, can effectively restrain the interference, optional instruction pulse smooth filtering, make the system in deceleration process smooth operation, increase the pulse signal digital filter and detection way.
Resonance inhibition: the servo drive can rise to inhibit resonance effect by adjusting the internal parameters
Encoder signal output: encoder signal frequency division and then drive output through line
Protection function: over voltage, over current, overload, overspeed and encoder anomaly and other kinds of error detection mechanism, nip in the bud.
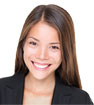


Category
Featured
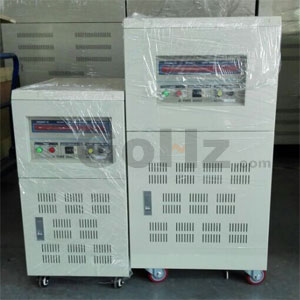
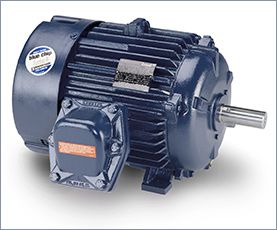
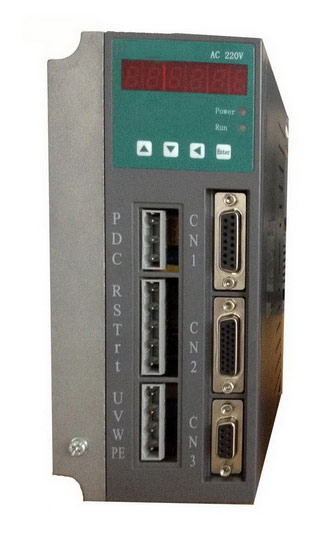