Why Motor Fails? Troubleshooting your motors

It is important during the selection process, the installation, the ensuing operation and maintenance, to focus on eliminating, or at least reducing, all potential causes of overheating.
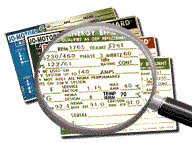
For example, every motor has nameplate information that defines its operating temperature range and its tolerance to temperature rise.
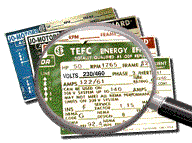
Adherence to voltage, phase and frequency tolerances insure that the "fuel"for the motor's operation will be as pure as possible.
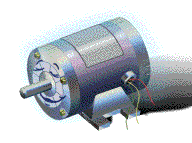
Regularly scheduled preventive maintenance that focuses on the motor's physical and electrical environment can help detect potential overheating problems.
Ultimately, any operation's goal is to produce the most using the least,saving as much as possible. Well thought out strategies that keep motors working longer help to meet the economic goals.
Ⅰ: Electrical
Voltage Unbalance
Voltage unbalance in a three-phase supply, frequently caused by plant equipment, causes excess temperature rise and, ultimately, motor failure. A 3.5percent voltage unbalance causes an approximately 25 percent temperature rise in the motor. Voltage should be checked frequently. If the cause of unbalance cannot be found, reduce the motor load or oversize the motor.
Single-Phase Operation
Single phase operation of a three phase motor can increase the current in the two remaining phases by a multiple of 1.73. All motors must have relays in the motor starter, usually one for each phase, to provide running protection.
Surge Voltages
Surge voltages may be caused by lightning. A liberal use of properly rated lightning rods having adequate ground connection minimize the potential damage of a system by lightning. Surge capacitors are also effective in this task. Surging from line switches and capacitors generally cause no problems as extensive as those of lightning surges.
Low or High Voltage
Low and high voltage are not often directly causal of motor failure, though they are frequently suspected. With good electrical systems and operating practice voltage at the motor under load will remain within ±5 percent of nameplate voltage. Although this is well within NEMA specifications, newer motors are easily damaged if operated consistently near a 5 percent voltage deviance.
Short Cycling
Short cycling is repeatedly starting a motor already up to operating temperature. Motor starting current is generally five to six times full load running current. Most motors manufacturers specify a safe range of starting frequency. It is important not to persist in violating these specifications.
Electrical Connections
Electrical connections should remain tight and secure at all times. A connection, if neglected, can quickly become loose enough to interrupt the circuit. This is particularly common where aluminum wire is used.
Ⅱ: Physical
Restricted Ventilation
Restricted ventilation causes a motor to operate at a higher than rated temperature, which is potentially damaging. Dirt, dust, chemicals, snow, oil, grass,and weeds are a few possible sources of clogging for an open frame motor. Open drip-proof and totally enclosed motors are safe from these obstructive materials. However, it is important not to install these motors where air flow maybe restricted, or within high ambient environments.
Improper Lubrication
Improper lubrication not only damages motor bearings, but often results in grease being thrown into the windings. All manufacturer's specifications as to frequency and type of lubrication should be followed with care.
Vibration
Vibration, belt tension, and misalignment are among the leading causes of motor failure. Mechanics must be adequately trained according to the latest procedures for proper maintenance in order to minimize the effects of vibration on all operating systems.
Overload
Motor overloading usually results from unusual alterations in the driven load. Broken gears or frozen bearings are also common overloading culprits. If running protection devices trip regularly, chronically disconnecting the motor from the operating line, locate and attend to the problem immediately. If a motor has a 1.15 Service Factor, do not run the motor at its 15 percent "cushion"factor continuously. This cushion exists only for temporary overloads.
Moisture
Condensation is often responsible for rust in otherwise protected totally enclosed motors. Moist air entering the vacuum created by the motor's heat condenses as the motor cools down. Good motor designs have a small drain hole in the bottom of the unit to allow the escape of condensed moisture.
If a motor is stored in a moist atmosphere, the insulation, even if it is non-hygroscopic, may lose some of its insulating properties. This is why motors should always be stored in a warm, dry place. Flooded motors should be thoroughly dried before being placed back into service. Electric heaters can be installed in large motors to regulate moisture by evaporation.
Ⅲ: Excessive Heat
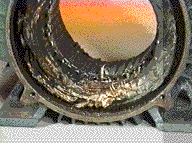
While excessive heat may be both causal and symptomatic of motor failure, the characteristic effect of excess heat is the accelerated breakdown of motor insulation. After overheating even once, a motor may run satisfactorily for awhile, but its useful life is cut short significantly. The most common causes of overheating are; the use of a motor with the wrong characteristics, poor cooling from obstructed ventilation devices, persistent overloading, excessive friction, and electrical overloads.
Ⅳ: Voltage Flicker
Starting motors with large loads causes voltage drop which is often evidenced by flickering lights. This flicker is objectionable only when the magnitude and frequency of the voltage drop exceed certain thresholds.
This threshold of objection is shown on a Voltage-Flicker curve. If the magnitude of the voltage drop and the frequency of occurrence lie below the threshold of perception, people generally do not notice any flicker.

Example: A five horsepower three phase motor is supplied by a 208 Volt feeder which also supplies 120 Volt lighting circuits. Assume that the feeder resistance = 0.06 ohms. For a 5 horsepower motor, the Full Load Amps (FLA) = 16amps. The motor starting current = 16 amps x 6 = 96 amps. V drop = starting current x feeder resistance = 96 amps x 0.06 ohms = 6 Volts.
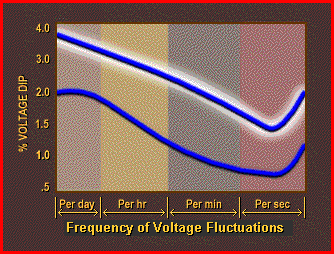
The 6 Volt drop along the feeder is equal to 5% of the voltage on the 120 Vlighting circuit, and it causes a noticeable flicker. If the motor is started once every hour, then the representative point, on the flicker curve is in the objectionable range. To correct this problem, supply the lighting circuits from a separate feeder, or reduce the voltage drop along the feeder. A reduced voltage starter often presents a very cost effective solution.
<- - Make a Comment - ->